Last year I made an HD fairing fit my Honda. I was intrigued by plastic welding and have been dabbling with it since. I have years of metal welding experience which basically is worth next to nothing for welding plastic.
Fast forward to March of this year I buy my XJ with a WJ5 on it. Its so noisy that I started pulling parts trying to eliminate noises coming from the fairing. I finally drop the Cycle sound which was falling apart and find a crack in the top of the dash over the headlight adjusting bolt. Also there is a .75 hole where the PO ran the wires for the cycle sound. There are cracks running parallel to the windshield. I cut a plug and welded it all up. I also find a couple cracks near the frame mounts and welded them up. I also drilled a set of mounting hole between the existing so that I have 6 bolts in the fairing instead of 4. Finally the fairing is quiet.
A month ago noticed the fairiing squeaking etc again. After inspection I find the old crack is back. I pulled the fairing and welded the crack again and this time ran a little extra filler rod and beefed up the area.
The other day on the bike again and noticed its getting loud again and sure enough the crack is back. Knowing that I've welded it 2x and its cracked again welding it a third time won't fix it. Time to do something different. When I bought my welding "kit" from Harbor Feight it included some stainless steel screen-wire. Decided to embed this and try vs getting ugly and riveting something over the area. FWIW the iron in the HF welding kit is junk.
In this picture the crack has been vee'd out with the iron in preparation for welding. You can tell from the texture I've worked here before
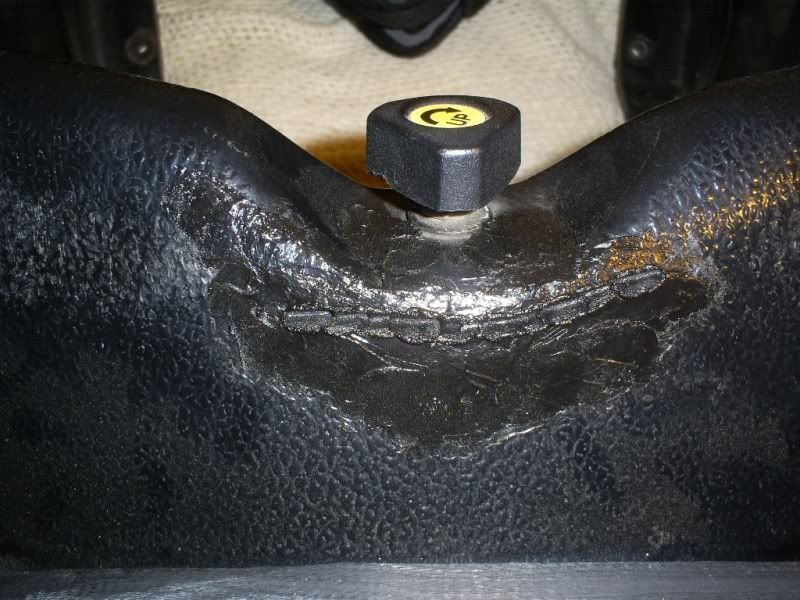
Here I've welded a couple places jumping around. There is a fine line between hot enough to weld and dimensionally unstable.
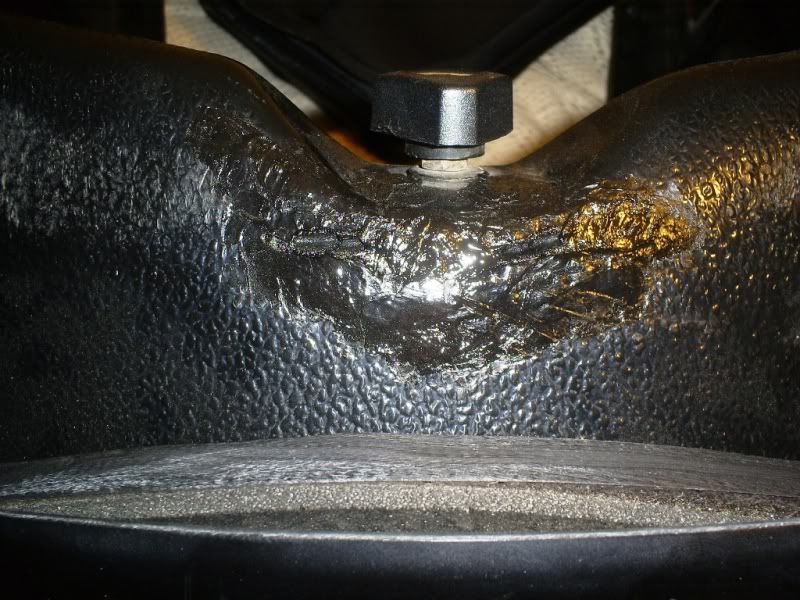
Weld complete with minimal extra filler
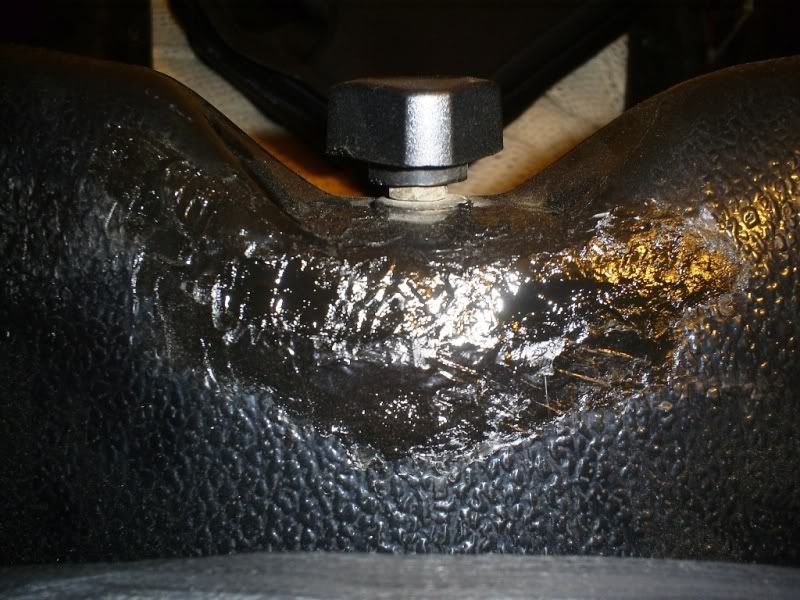
SS screenwire tacked in place
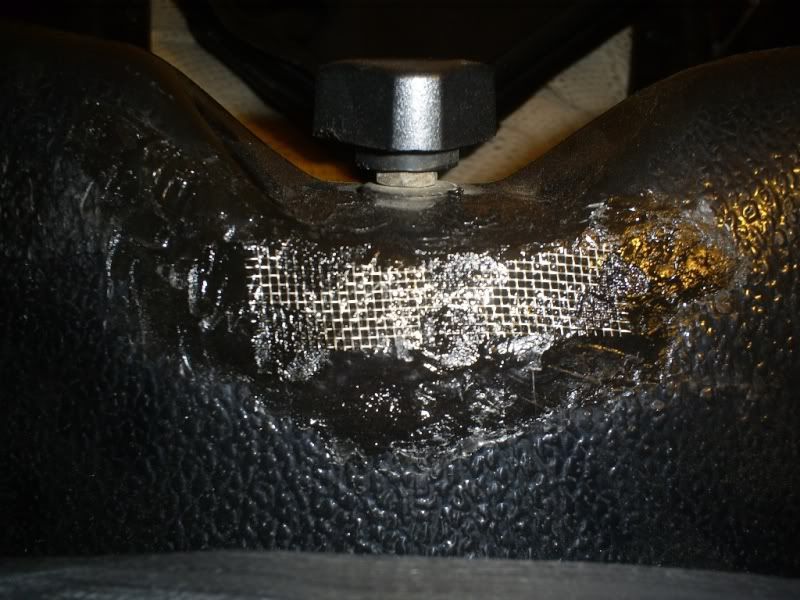
Here the screen wire is embedded although a little shallow. The material is not that thick to begin with and the heat on the screen transfers out making larger areas unstable. You have to keep moving.
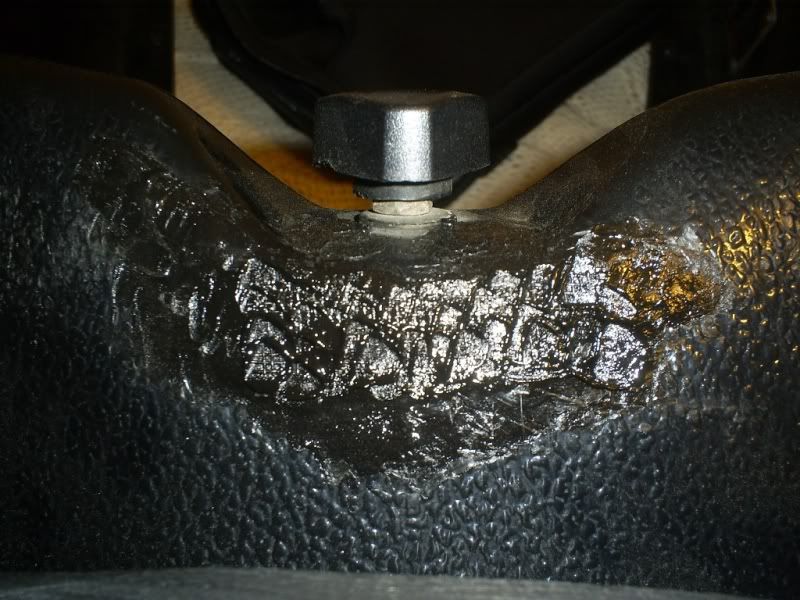
Finished weld. I ran a piece of filler rod over this area to again beef it up a little. Have to keep moving as once the area is too hot its quite unstable.
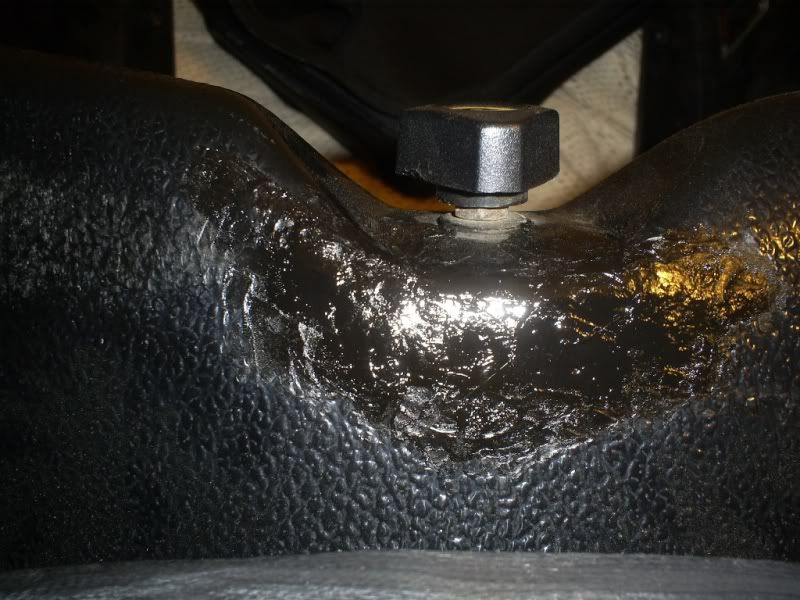
The view from a little further back. Still doesn't look too bad. Time will tell.
Fast forward to March of this year I buy my XJ with a WJ5 on it. Its so noisy that I started pulling parts trying to eliminate noises coming from the fairing. I finally drop the Cycle sound which was falling apart and find a crack in the top of the dash over the headlight adjusting bolt. Also there is a .75 hole where the PO ran the wires for the cycle sound. There are cracks running parallel to the windshield. I cut a plug and welded it all up. I also find a couple cracks near the frame mounts and welded them up. I also drilled a set of mounting hole between the existing so that I have 6 bolts in the fairing instead of 4. Finally the fairing is quiet.
A month ago noticed the fairiing squeaking etc again. After inspection I find the old crack is back. I pulled the fairing and welded the crack again and this time ran a little extra filler rod and beefed up the area.
The other day on the bike again and noticed its getting loud again and sure enough the crack is back. Knowing that I've welded it 2x and its cracked again welding it a third time won't fix it. Time to do something different. When I bought my welding "kit" from Harbor Feight it included some stainless steel screen-wire. Decided to embed this and try vs getting ugly and riveting something over the area. FWIW the iron in the HF welding kit is junk.
In this picture the crack has been vee'd out with the iron in preparation for welding. You can tell from the texture I've worked here before
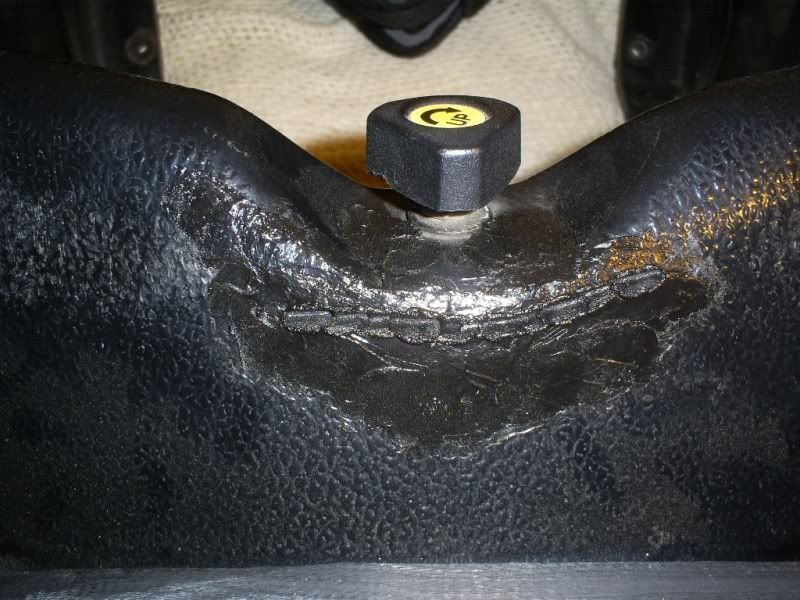
Here I've welded a couple places jumping around. There is a fine line between hot enough to weld and dimensionally unstable.
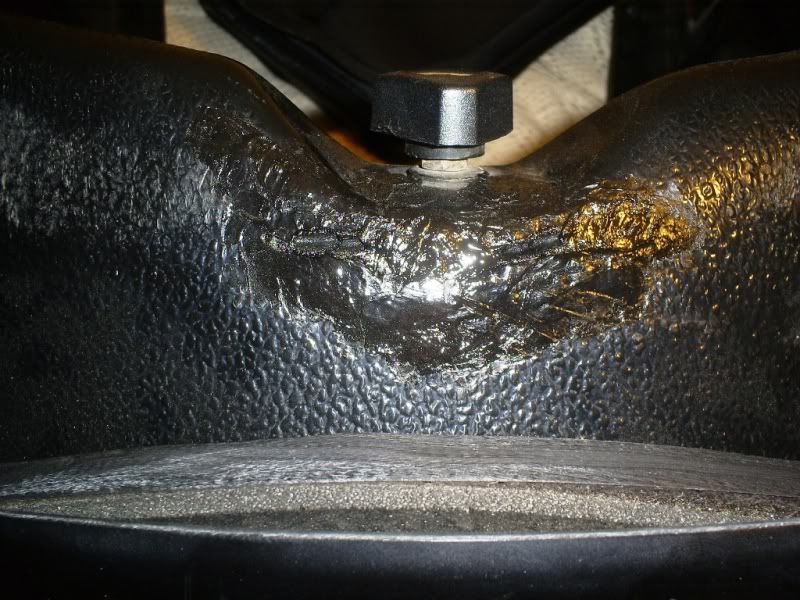
Weld complete with minimal extra filler
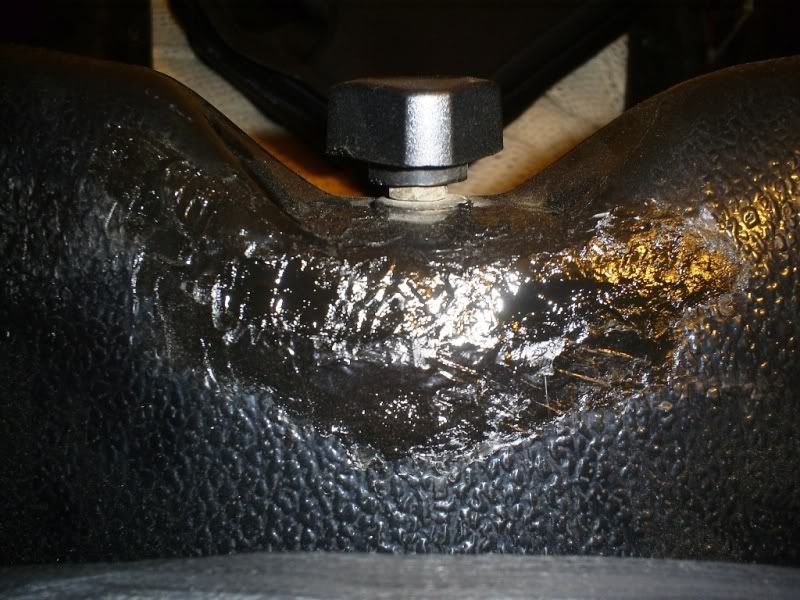
SS screenwire tacked in place
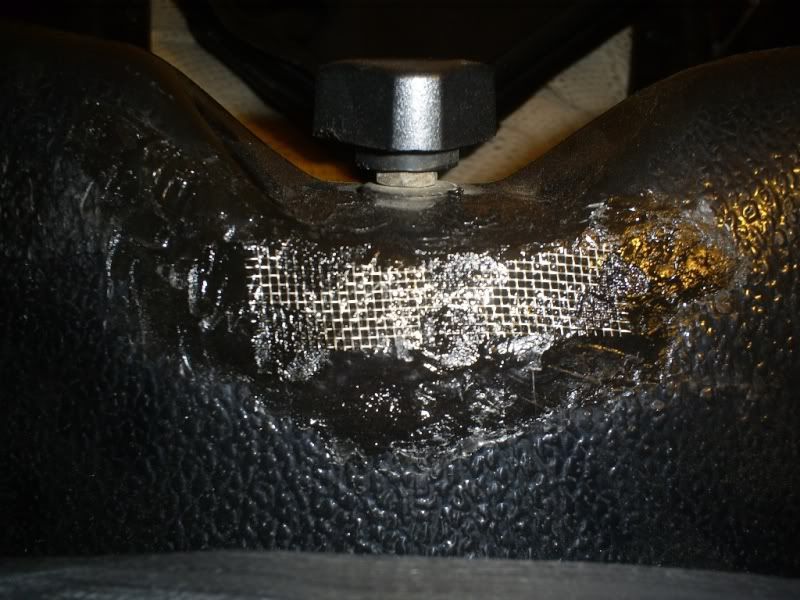
Here the screen wire is embedded although a little shallow. The material is not that thick to begin with and the heat on the screen transfers out making larger areas unstable. You have to keep moving.
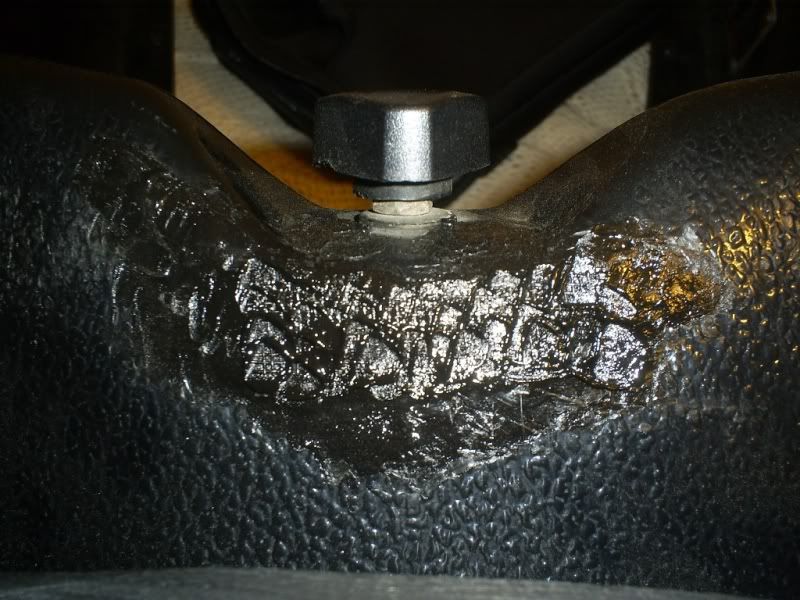
Finished weld. I ran a piece of filler rod over this area to again beef it up a little. Have to keep moving as once the area is too hot its quite unstable.
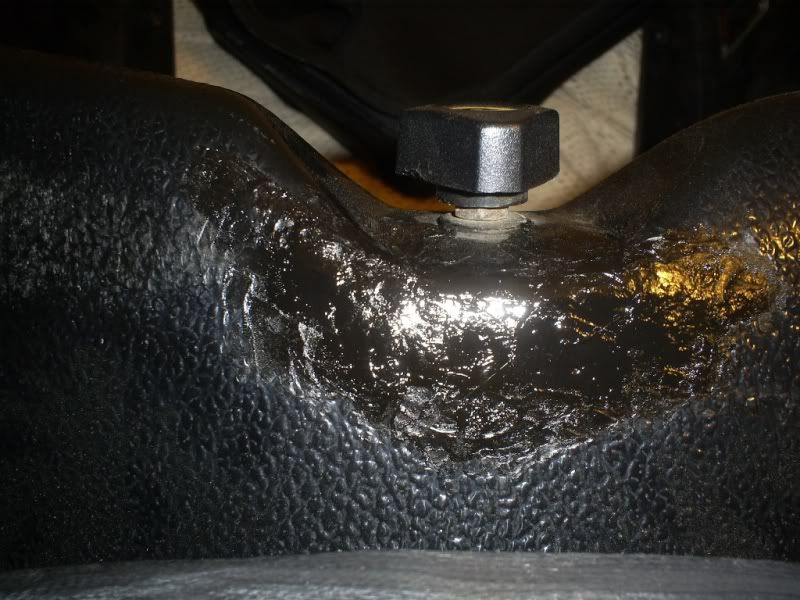
The view from a little further back. Still doesn't look too bad. Time will tell.
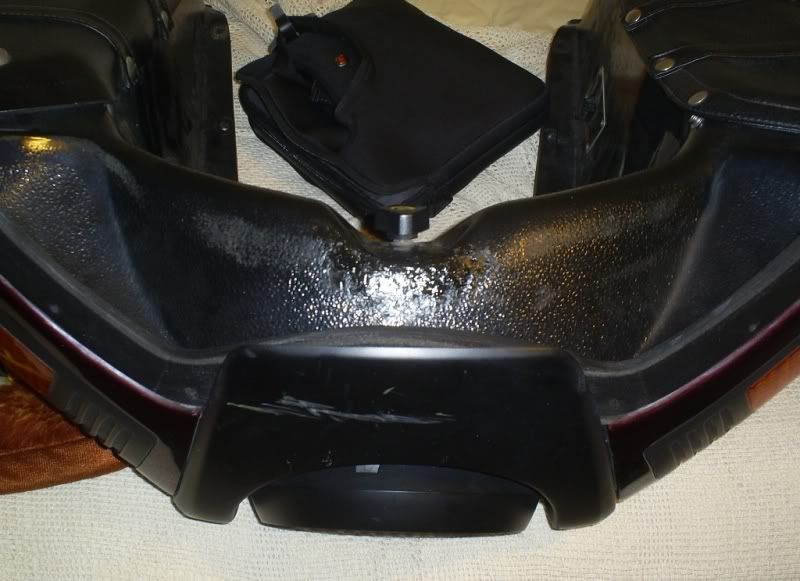
Comment