Time to Chime in.
Hey guys,
Interesting tech discussion here, thanks.
I used washers, because that's what I had on hand with this PROTOTYPE proof of concept fitment. I plan on replacing them behind the pulley with a piece of 1/2" thick aluminum plate drilled/machined to size. The PULLEY from Grainger is ZAMAK #3, pretty strong cast aluminum/zinc alloy. Also the 10mm x 100mm bolt is Metric Grade 8.8 = Standard Grade 5 at 120,000 psi tensile strength..again, I think plenty strong to secure the very snug pulley to bolt shaft fitting against the ROTOR.
The ROTOR is quite heavy and well balanced already. The pulley is balanced as stated to 3600 rpm, so should be able to handle 7200 or more. I don't have a way to test how much tension is being put on the belt/pulley at the crank. With the heavy ROTOR acting as a flywheel, I would think it would actually help reduce the amount of perpendicular stress on the bearings induced by the belt's tension, and since it's a LOW DRAG ALT...it's meant for a race car application...least drag necessary=more HP to wheels...that the belt tension doesn't need to be terribly tight, it's a 1/2" wide belt, has plenty of grip with very little tension on it.
Here's some interesting photos I had from a fellow that posted these way back in 2002 or 3. This is the highest resolution of the images I had, and so I can't see that well the center of the crank hub, but from the looks of the CUSTOM made Supercharger and plates $$$, that he's probably custom made a pulley HUB $$$ to mount onto the end of the crank/Rotor combo since he's keeping the OEM ALT cover...just made a hole in the center!
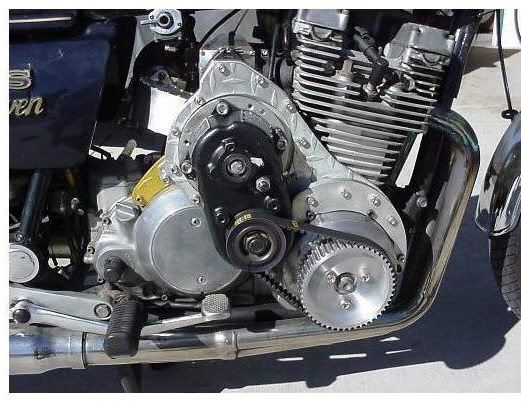
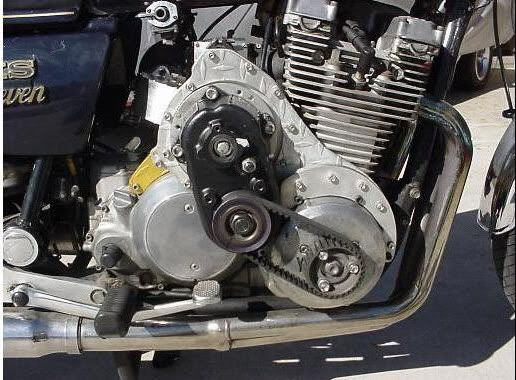
I checked into the timing belt style recently, some findings: The round slot style was shown to withstand stresses and be stronger than the trapezoidal or square cut slots.
The AUTO sized round "Radius Tooth HTD" spacing is 20mm center of tooth to tooth, and althouth they offer pulleys for Alternators...the Mini-Alt has a shaft ID of ~17mm/0.670"...the don't offer a similar sized pulley for the crank..they are all at least 0.50" or larger ID/Bore sizes...too big for the 10mm bolt. These toothed pulleys were found on a RACING PARTS site, and just the ALT pulley is over $60.00, not to mention the GUIDES were ~$30.00.
The Econobelt and places I've seen with pulleys, have the Radius Tooth spacing at 8mm max! Then there's the problem of if you find a pulley with an ID bore size to fit the ALT, it's extremely LARGE Outer diameter size, and the ones to fit the crank's ID of 10mm...I could only find either 8mm or 12 mm, then they are very small or about the same size we have now, but you can't get a matching one for the ALT's Shaft!
The ALT came with the V-groove, and I was able to find/source a comparable sized pulley that would fit with the use of the 10mm bolt for the crank/rotor location. Again, my goal was to be able to do this with the least $$ expendable, with off the shelf parts, tools, and prices for most budgets.
I'm awaiting the receipt of the larger PLATE piece to redo the mount, positioning the ALT another 1/4" forward away from the clutch cable, and then to afix the better belt/pulley cover. The weather is getting a bit warmer and nicer...spring is starting to spring here, and with the soaring fuel prices...I may be forced to turn Godzilla into a daily work/commuter at 30mpg vs. my SUV's 18 !
So...I may be giving this design a longer test run sooner than I anticipated!
I will say though, if anyone can source the radius toothed pulleys in the 2-3" overall diameter size and have the required ID's of 10mm AND 17mm for the crank and ALT, tell me where and I'll be happy to acquire the parts. I know they make the belts in the ~20"...508mm length size needed with a ~2.75" diam set of crank/alt pulleys.
T.C.
Hey guys,
Interesting tech discussion here, thanks.
I used washers, because that's what I had on hand with this PROTOTYPE proof of concept fitment. I plan on replacing them behind the pulley with a piece of 1/2" thick aluminum plate drilled/machined to size. The PULLEY from Grainger is ZAMAK #3, pretty strong cast aluminum/zinc alloy. Also the 10mm x 100mm bolt is Metric Grade 8.8 = Standard Grade 5 at 120,000 psi tensile strength..again, I think plenty strong to secure the very snug pulley to bolt shaft fitting against the ROTOR.
The ROTOR is quite heavy and well balanced already. The pulley is balanced as stated to 3600 rpm, so should be able to handle 7200 or more. I don't have a way to test how much tension is being put on the belt/pulley at the crank. With the heavy ROTOR acting as a flywheel, I would think it would actually help reduce the amount of perpendicular stress on the bearings induced by the belt's tension, and since it's a LOW DRAG ALT...it's meant for a race car application...least drag necessary=more HP to wheels...that the belt tension doesn't need to be terribly tight, it's a 1/2" wide belt, has plenty of grip with very little tension on it.
Here's some interesting photos I had from a fellow that posted these way back in 2002 or 3. This is the highest resolution of the images I had, and so I can't see that well the center of the crank hub, but from the looks of the CUSTOM made Supercharger and plates $$$, that he's probably custom made a pulley HUB $$$ to mount onto the end of the crank/Rotor combo since he's keeping the OEM ALT cover...just made a hole in the center!
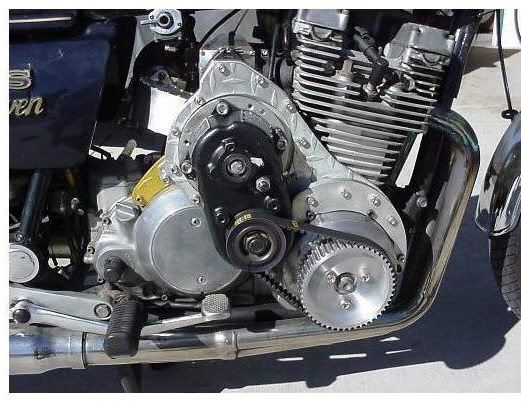
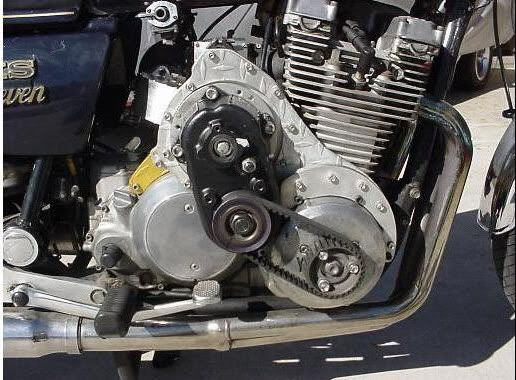
I checked into the timing belt style recently, some findings: The round slot style was shown to withstand stresses and be stronger than the trapezoidal or square cut slots.
The AUTO sized round "Radius Tooth HTD" spacing is 20mm center of tooth to tooth, and althouth they offer pulleys for Alternators...the Mini-Alt has a shaft ID of ~17mm/0.670"...the don't offer a similar sized pulley for the crank..they are all at least 0.50" or larger ID/Bore sizes...too big for the 10mm bolt. These toothed pulleys were found on a RACING PARTS site, and just the ALT pulley is over $60.00, not to mention the GUIDES were ~$30.00.

The Econobelt and places I've seen with pulleys, have the Radius Tooth spacing at 8mm max! Then there's the problem of if you find a pulley with an ID bore size to fit the ALT, it's extremely LARGE Outer diameter size, and the ones to fit the crank's ID of 10mm...I could only find either 8mm or 12 mm, then they are very small or about the same size we have now, but you can't get a matching one for the ALT's Shaft!

The ALT came with the V-groove, and I was able to find/source a comparable sized pulley that would fit with the use of the 10mm bolt for the crank/rotor location. Again, my goal was to be able to do this with the least $$ expendable, with off the shelf parts, tools, and prices for most budgets.
I'm awaiting the receipt of the larger PLATE piece to redo the mount, positioning the ALT another 1/4" forward away from the clutch cable, and then to afix the better belt/pulley cover. The weather is getting a bit warmer and nicer...spring is starting to spring here, and with the soaring fuel prices...I may be forced to turn Godzilla into a daily work/commuter at 30mpg vs. my SUV's 18 !


I will say though, if anyone can source the radius toothed pulleys in the 2-3" overall diameter size and have the required ID's of 10mm AND 17mm for the crank and ALT, tell me where and I'll be happy to acquire the parts. I know they make the belts in the ~20"...508mm length size needed with a ~2.75" diam set of crank/alt pulleys.
T.C.
Comment