So today I decided to repair a float post. No2 carb had a broken float post on the SG I bought (which I knew when I purchased it). When I opened the carb, the break was actually pretty nasty looking.
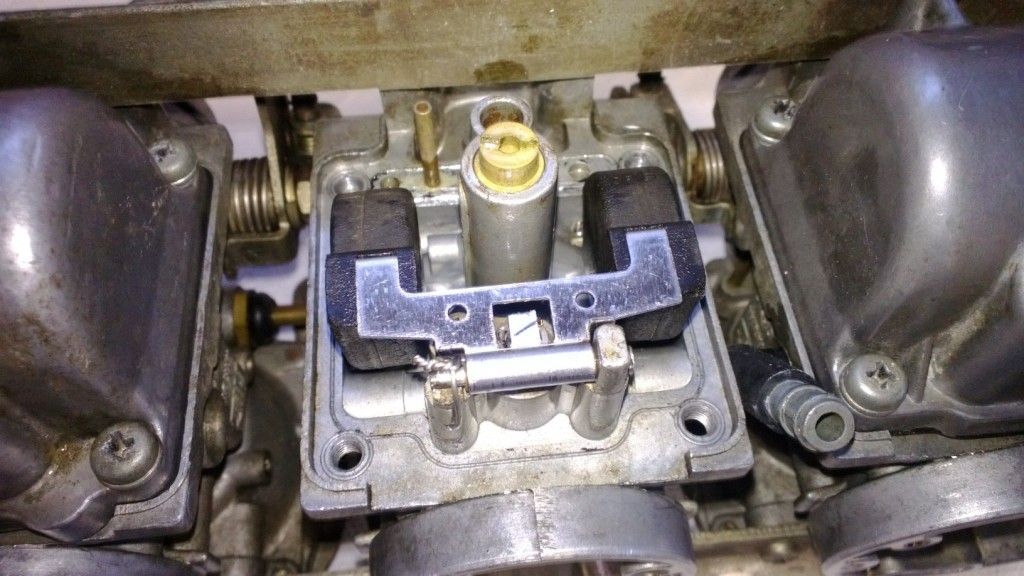
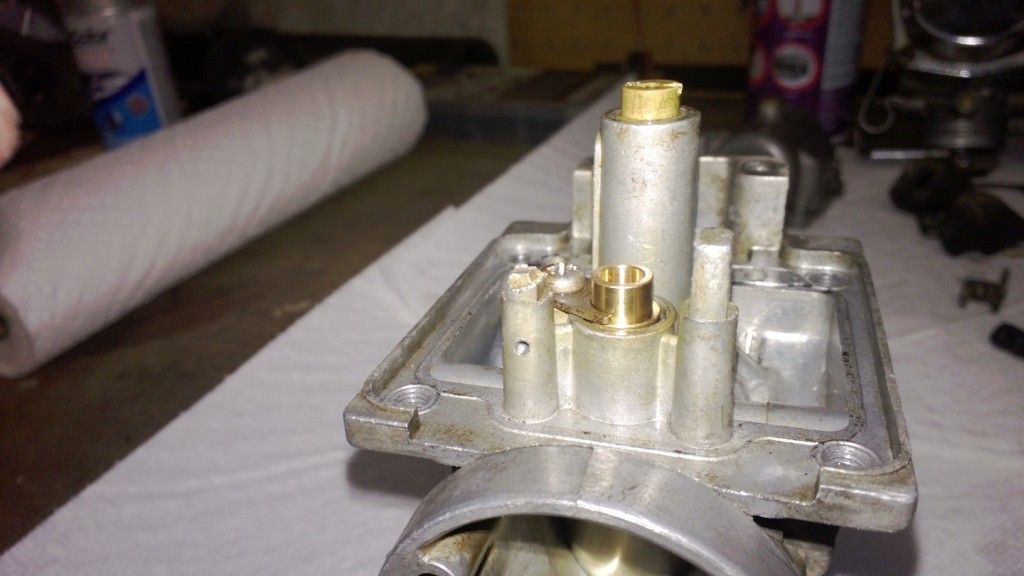
It had run decent with the condition, but I had that one carb flooding after the clean up I had done, so rather than wait and see if it cleared up I decided to fix it.
Now I had always planned to use a shoulder bolt, thread it into the post that remained, and cut flat spots in it and drill a hole, so once it was threaded in, it would work as a float post. Well, it just so happens that I have a spare carb body for the 80-81 style carbs with stripped out threads in the mix screw tower. So I consider it scrap material. Thinking this out a bit, I decided to cut off the float post close to the reinforcing rib from the needle valve “tower”. Then cut the carb to be repaired in a similar place, such that after allowing for the width of the blade, the two would join to be the same height.
After carefully cutting both post, I center punched the carb body, and drilled a hole for a 8-32 tap. Then tapped out the hole as best I could. Then put the screw into the hole.
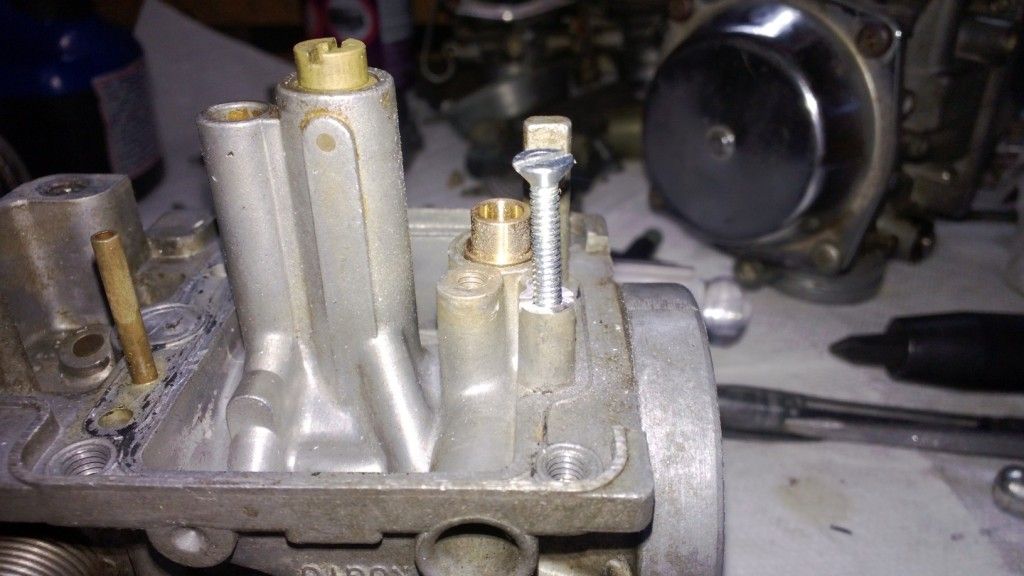
Next was to tap the piece of float post. To do that, I took a piece of wood, and drilled holes to match the stepped down top section so it pushed in and was solidly mounted. Now I drilled and tapped that piece. After measuring how deep the bolt went into each piece, I knew how long to cut the bolt to. Now I threaded it into the top piece of the post.
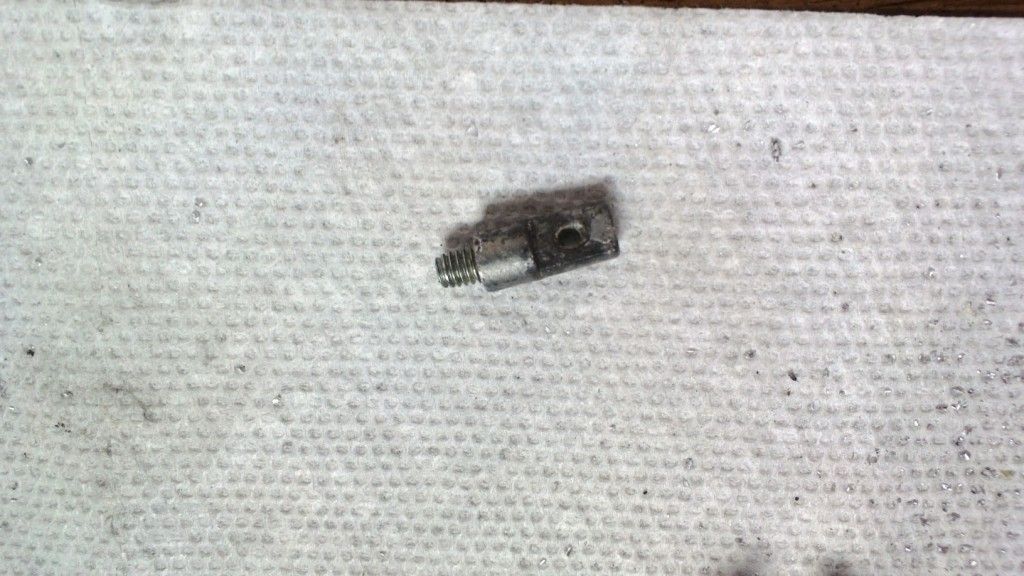
Of course, next step is to thread it into the body section.
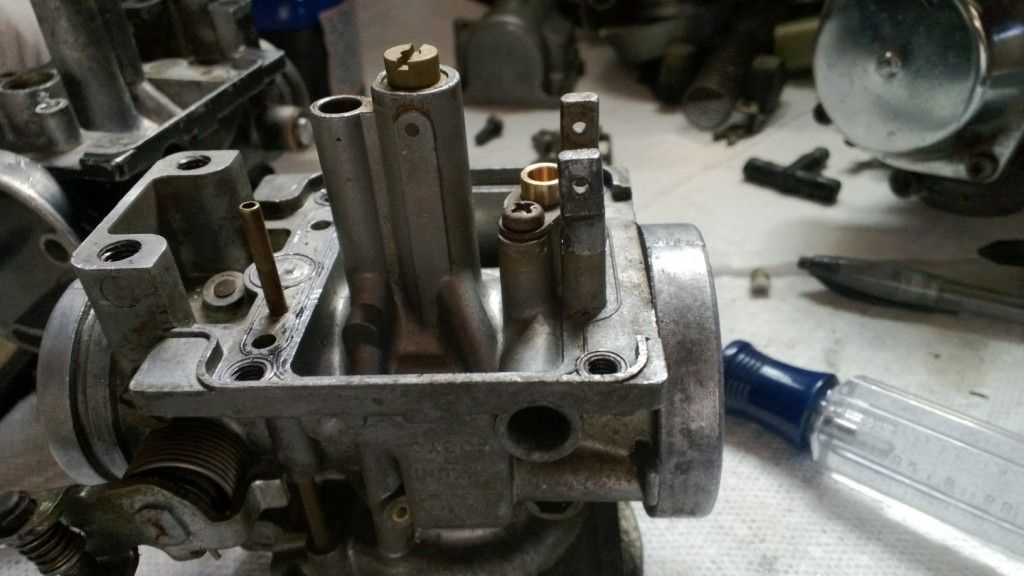
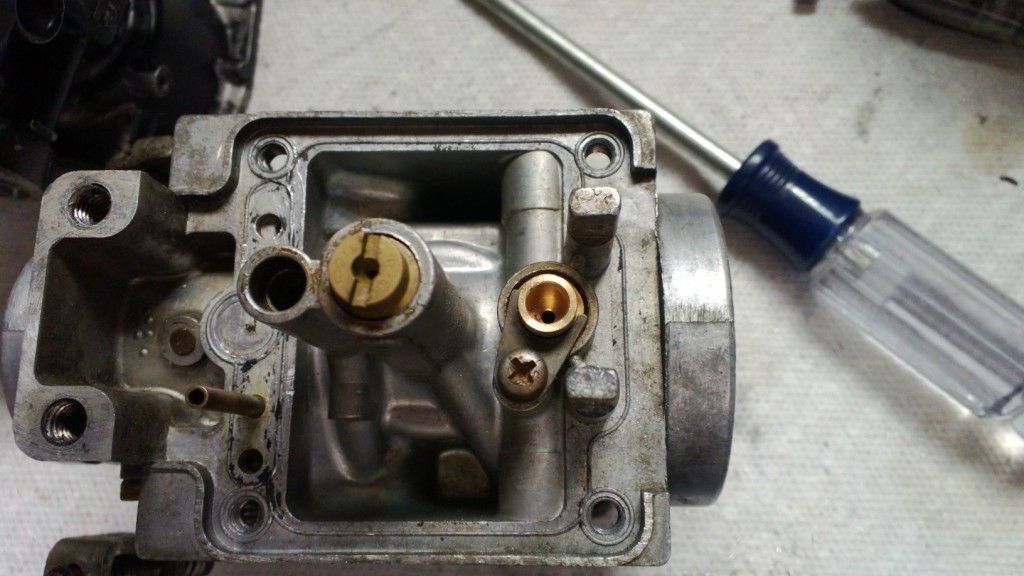
The discerning eye will notice it does not 100% align, but it is dang close. If I did this again, I would use a drill press instead of hand drill. So, now I have a almost factory float post again, it works great, Go the float installed, height set, and the movement is good.
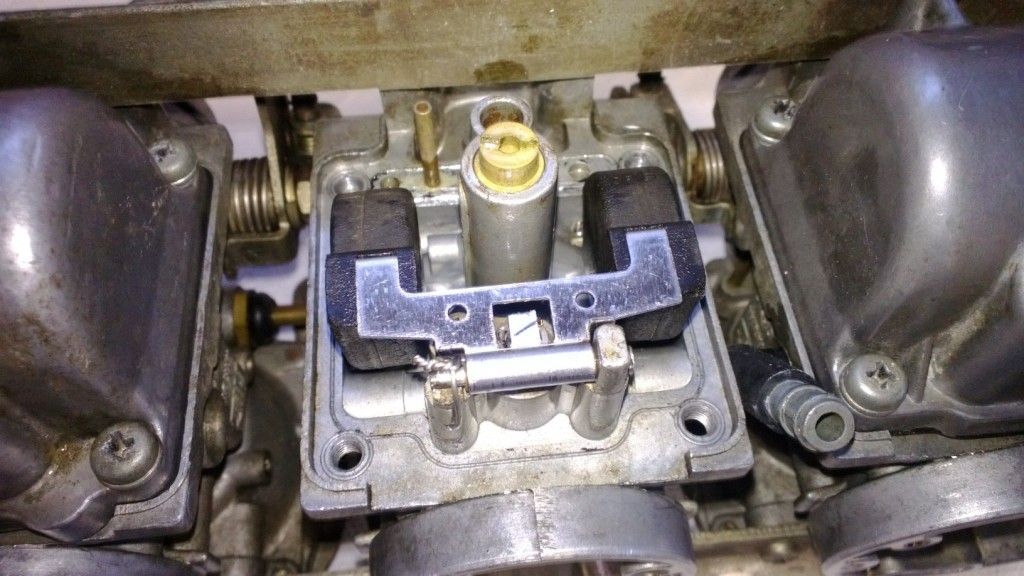
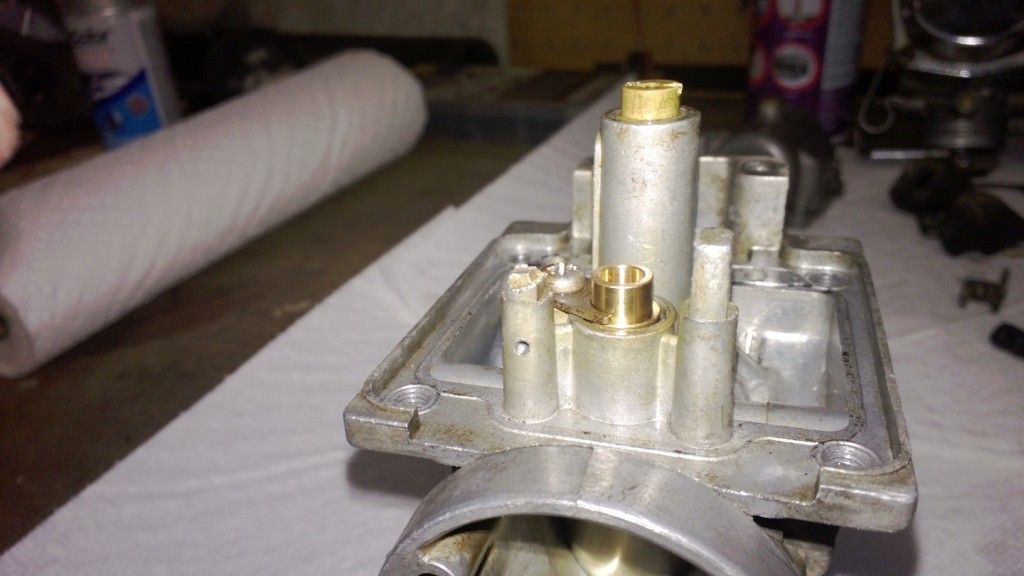
It had run decent with the condition, but I had that one carb flooding after the clean up I had done, so rather than wait and see if it cleared up I decided to fix it.
Now I had always planned to use a shoulder bolt, thread it into the post that remained, and cut flat spots in it and drill a hole, so once it was threaded in, it would work as a float post. Well, it just so happens that I have a spare carb body for the 80-81 style carbs with stripped out threads in the mix screw tower. So I consider it scrap material. Thinking this out a bit, I decided to cut off the float post close to the reinforcing rib from the needle valve “tower”. Then cut the carb to be repaired in a similar place, such that after allowing for the width of the blade, the two would join to be the same height.
After carefully cutting both post, I center punched the carb body, and drilled a hole for a 8-32 tap. Then tapped out the hole as best I could. Then put the screw into the hole.
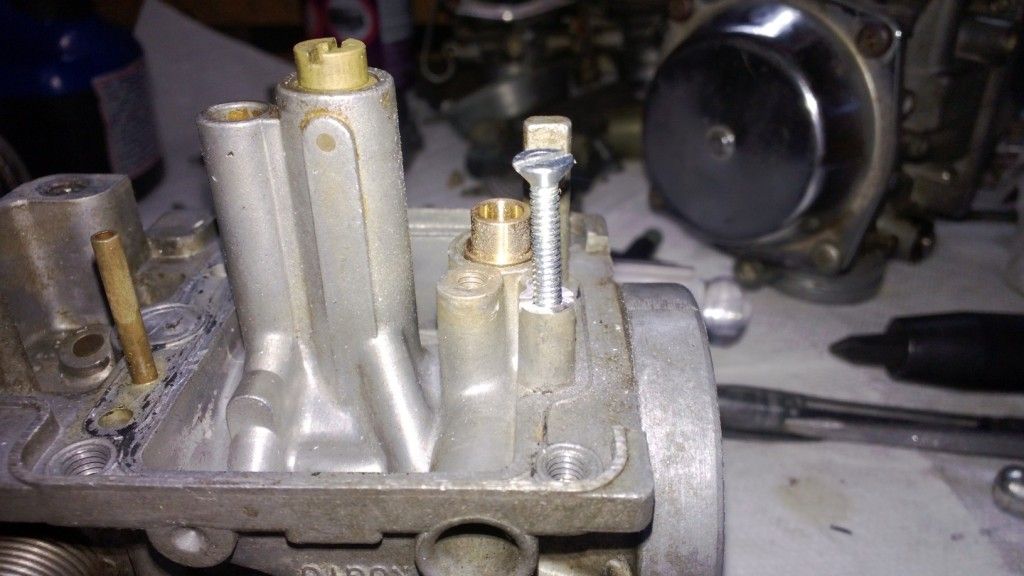
Next was to tap the piece of float post. To do that, I took a piece of wood, and drilled holes to match the stepped down top section so it pushed in and was solidly mounted. Now I drilled and tapped that piece. After measuring how deep the bolt went into each piece, I knew how long to cut the bolt to. Now I threaded it into the top piece of the post.
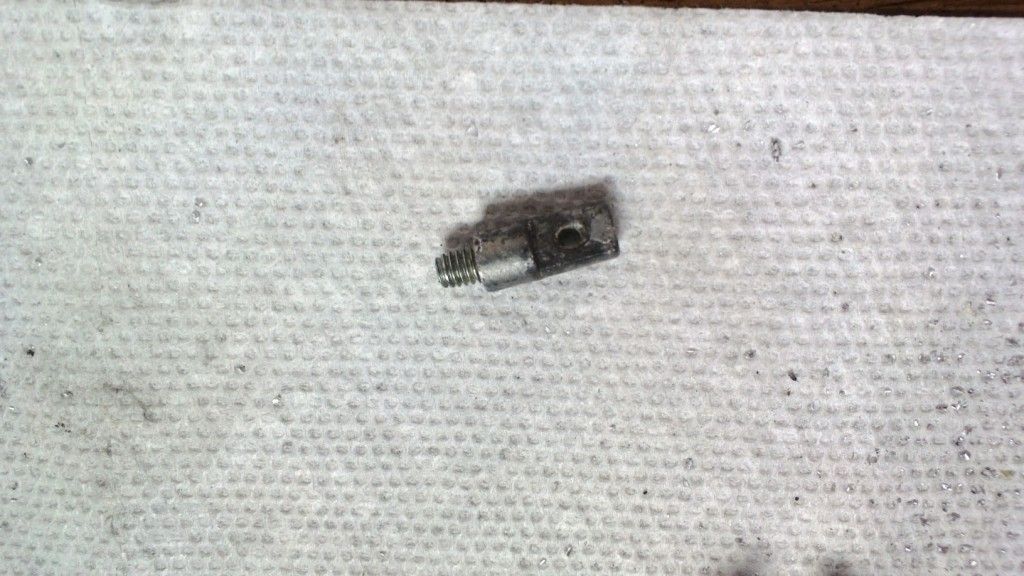
Of course, next step is to thread it into the body section.
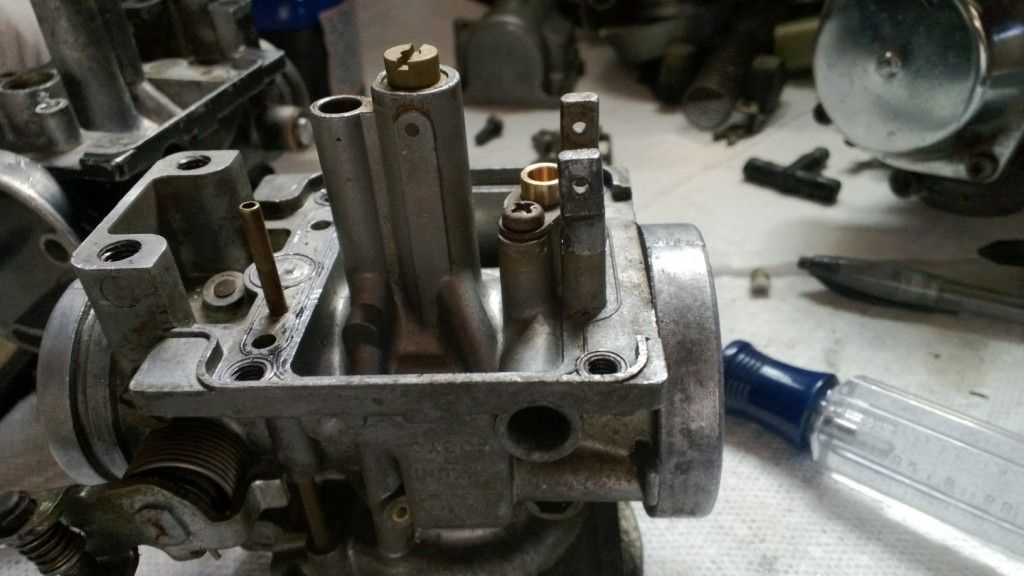
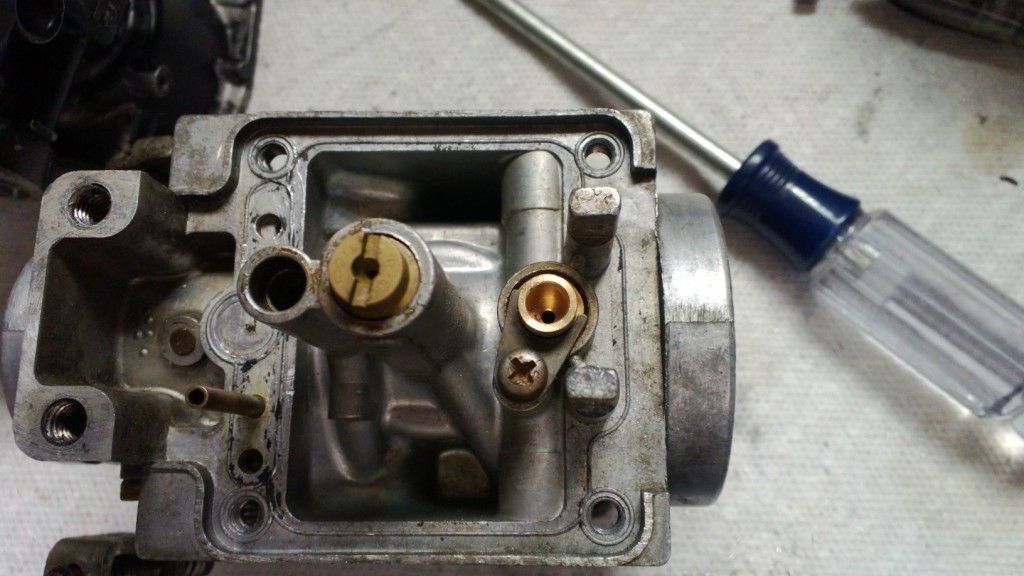
The discerning eye will notice it does not 100% align, but it is dang close. If I did this again, I would use a drill press instead of hand drill. So, now I have a almost factory float post again, it works great, Go the float installed, height set, and the movement is good.
Comment