... are still a bad idea. Those who have been around a while will remember this thread...http://www.xs11.com/forum/showthread...ighlight=crimp where we beat the subject to death. Good reading if you haven't seen it.
Here's the proof...
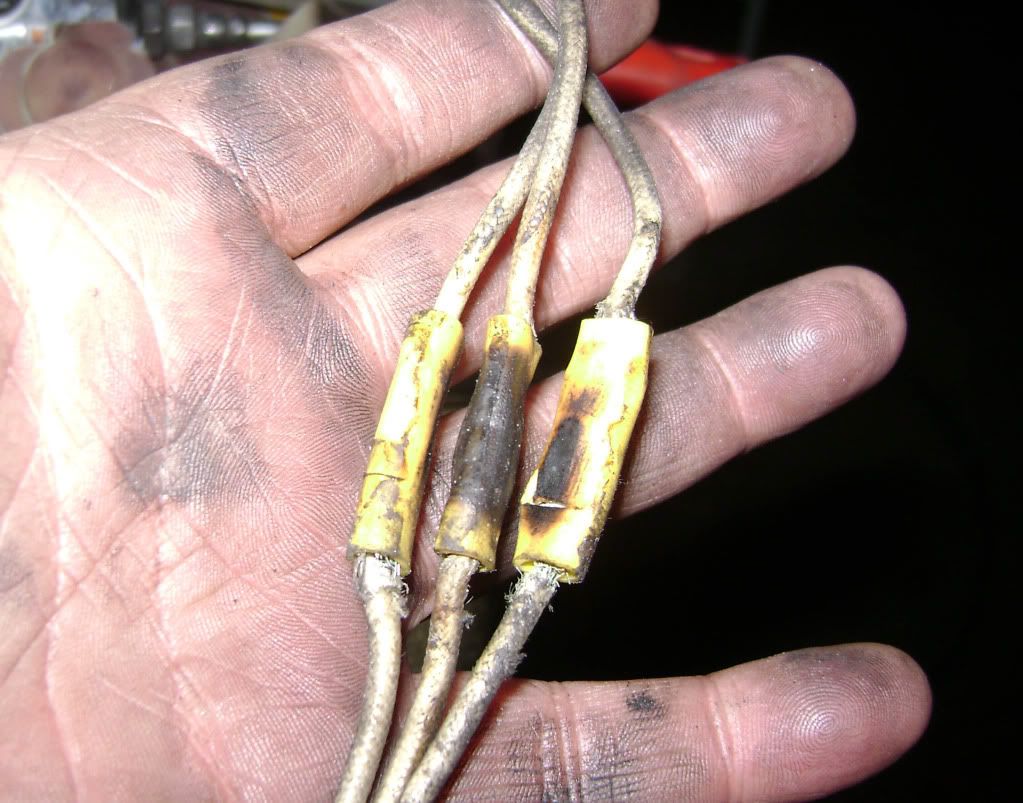
Spliced into the stator leads from the alternator, these got a little hot....
Here's the proof...
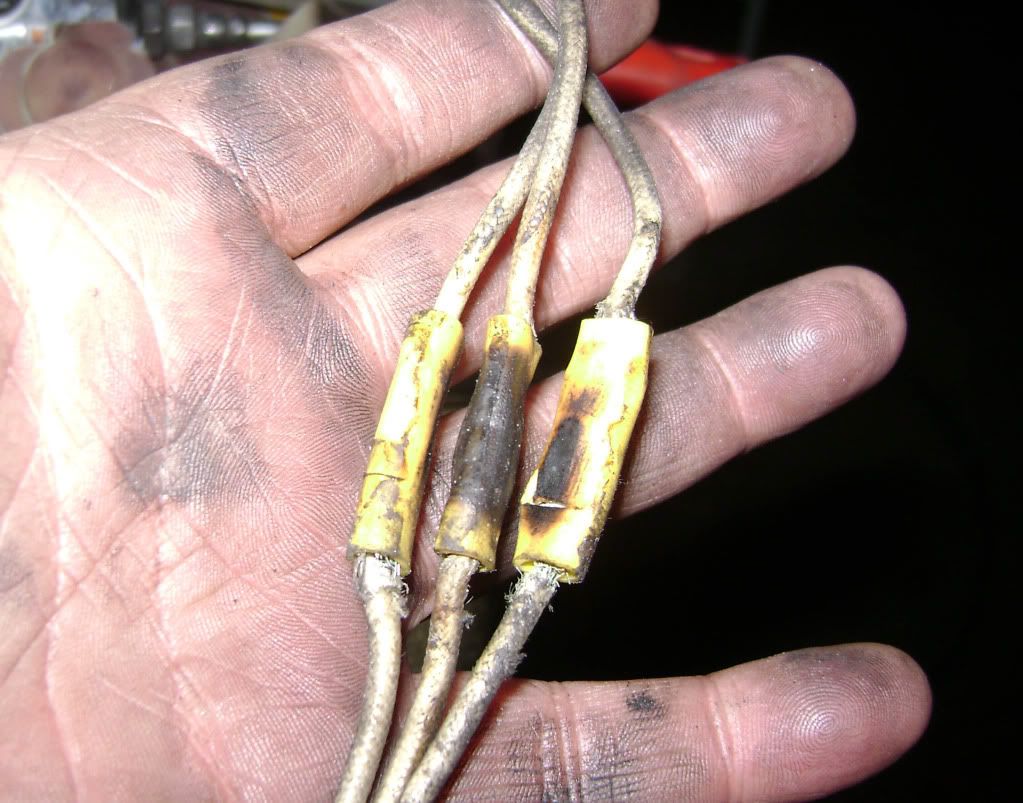
Spliced into the stator leads from the alternator, these got a little hot....

Comment