Just for general consumption. I had a Master Cylinder with a nicked bore. In machining we often use a flapper rod and die grinder to "buzz" it out. Saw a slot centered in a straight metal rod (bigger bores need bigger rods). Clamp the part in a vise or fixed somehow so it won't spin on you. Work with smooth strokes and you can "hone" a cylinder IF it is not too bad. Stop the grinder before exiting the bore!
Use one hand to steady the rod and practice on a POS before moving to the job. By using progressive grits (180,240,320,etc.) of cloth backed sand paper you can save a bore without the expense of various hones. A good variable speed die grinder is essential. I have buzzed out up to 12 inch bores. Note the rod in the pic is 1/4" and I buzzed out a 11/16 bore. It is critical to wrap the sandpaper around the rod tightly with minimal clearance between it and the bore size. Insert fully with a twist motion prior engaging the die grinder. You can also use scotchbrite for cleanup operations.


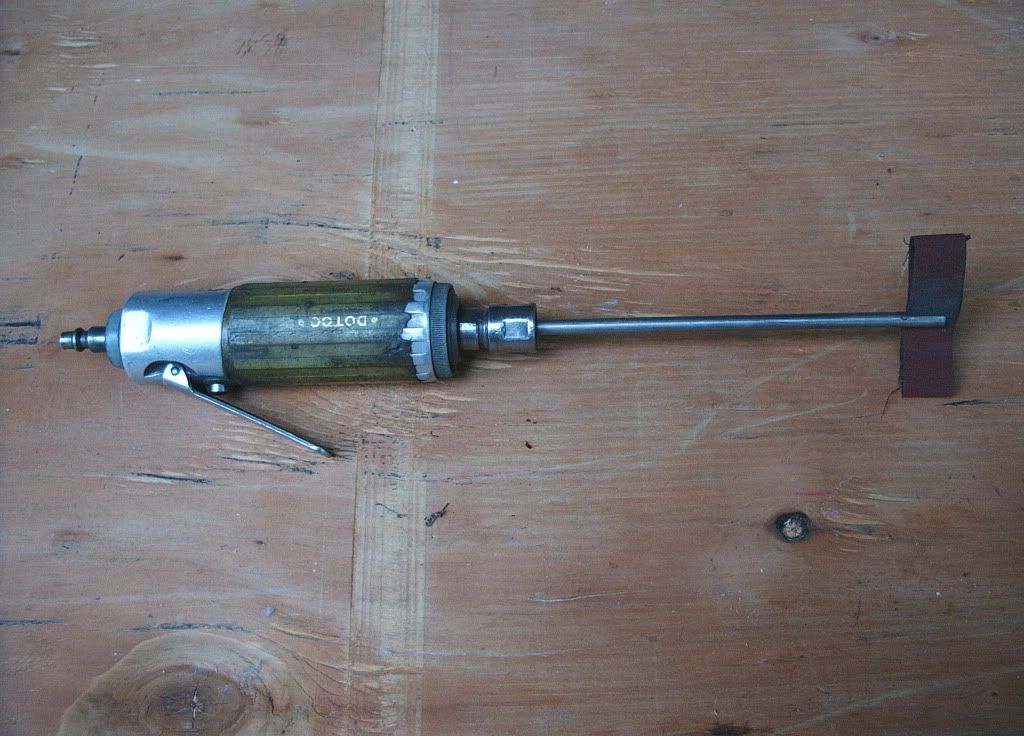
Comment