This is about drilling out a fork leg (aluminum) that uses a 15mm axle to fit a 17mm axle. First, there is plenty of meat on the leg to embiggen the hole. Problem is, there is a pinch bolt on each leg, so there is a slot in the hole, as in the drawing below. I am guessing that the drill bit would catch on this slot causing difficulty. If I tighten the bolt so the slot is closed, im guessing it should drill fine. The next size down from 17mm would be a 21/32 (16.669mm), and down another size would be 16.5mm, then 41/64 (16.272mm). Anyone have any wisdom they'd wanna share on how to do this?
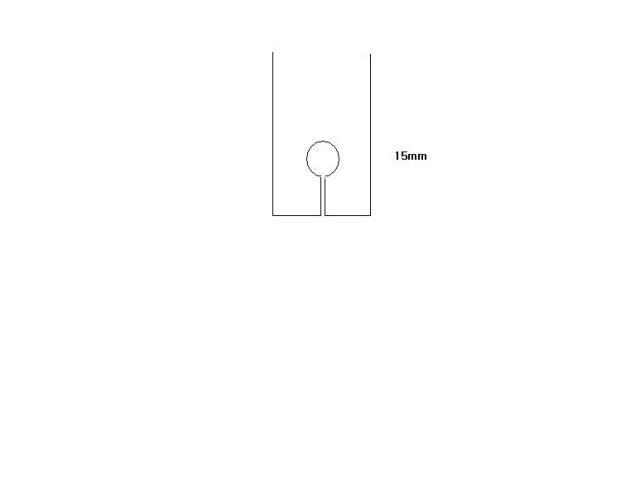
Comment