It's looking a little battle weary now but this is what i've been using for the last 12 years, and it's taken on some pretty serious projects. Car trailers, Horse trailers, Bike hauling trailers, Steel portal framing for sheds, etc. I use it both with and without gas, gas for larger projects (the wire is cheaper) and no gas for small jobbing work. I use a wire feed lubricant by way of an impregnated felt block at the feed end and get a consistant smooth feed, and welds. With proper preparation, a root weld and mutliple runs it will happily weld up to 8mm (5/16") but I also have a stick welder and tend to use that on the thicker metals. I use an auto dark helmet. The handpeice is a Miller knock off, so tips are easy to get. The brand is Weldwell and is based around a high quality NZ made transformer. http://www.weldwell.co.nz/Default.aspx?Page=Home&Load=1 (Not much help to you guys in the states, but i'm not sure you would get the same result from a chinese made transformer) Who makes Chicago Electric?
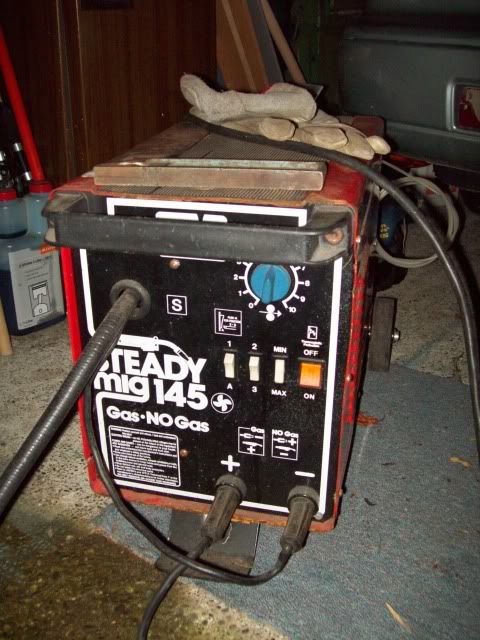
Comment